7 Steps in the Manufacturing Process of Corrugated Boxes: Explained

The Journey of Corrugated Box Manufacturing : From Raw Materials to Final Product
Corrugated boxes are everywhere. They carry our groceries, protect our electronics, and serve as the backbone of e-commerce. But have you ever wondered about the journey they take before reaching us? Understanding how these boxes are made unveils a story of ingenuity, innovation, and sustainability.
This comprehensive guide explores the seven key stages in the life of a corrugated box. From humble beginnings as raw paper to becoming indispensable tools in logistics, let’s delve into the fascinating manufacturing process.
While they might seem like simple packaging solutions, corrugated boxes are intricate products born of cutting-edge engineering, environmental consciousness, and design innovation. They protect your goods during shipping, display your brand in stores, and, increasingly, help reduce environmental impact.
This blog extends the story of these indispensable packaging products, focusing on innovations, challenges, and the pivotal role they play across industries.
Step 1: Sourcing Raw Materials – A Sustainable Foundation
Raw Materials: Paper and Beyond
The manufacturing process begins with selecting high-quality linerboard and medium paper. Linerboard provides the exterior strength and printability, while the medium, often sourced from recycled materials, creates the structural flutes.
Impact of Recycling
Every ton of recycled paper saves approximately 17 trees, 7,000 gallons of water, and significant energy. This means that the corrugated box industry not only meets packaging needs but also contributes positively to resource conservation.
Innovative Alternatives
In response to sustainability challenges, some manufacturers are exploring agricultural by-products like wheat straw or sugarcane bagasse as alternative raw materials. These innovations reduce dependence on traditional forestry.
Sourcing Raw Materials: The Heart of the Box
The life of a corrugated box begins with its foundation: paper. High-quality linerboard and medium form the essential layers.
Linerboard and Medium: The Dynamic Duo
- Linerboard: The sturdy outer layer, responsible for durability and printability.
- Medium: The fluted interior, acting as the box’s backbone by providing structure and cushioning.
These papers are sourced from sustainable forestry or recycled materials, reflecting a shift towards eco-conscious production. Manufacturers balance raw wood fibers with recycled content, ensuring strength while reducing environmental impact.
Sustainability Spotlight
Did you know that over 90% of corrugated materials in the U.S. are recovered for recycling? This statistic highlights the industry’s commitment to sustainability, driven by consumer demand for green solutions.

Step 2: Creating the Corrugated Medium – Engineering Strength
Fluting’s Role in Physics
The wavy shape of the corrugated medium isn’t just for aesthetics. It uses the principles of engineering to distribute weight efficiently and absorb shock. This explains why corrugated boxes can hold heavy items without collapsing.
Custom Flute Profiles
Different flute sizes cater to diverse needs:
- A-Flute: Best for cushioning fragile items.
- B-Flute: Common in retail packaging for its compactness.
- E-Flute: Favored for luxury packaging due to its thin profile.
The Role of Starch-Based Adhesives
Eco-friendly adhesives, primarily made from cornstarch, bind the medium and linerboard. These adhesives are biodegradable, aligning with the industry’s green goals.
Making the Corrugated Medium: Engineering the Flutes
Fluting is what sets corrugated boxes apart from regular cardboard. This step involves turning processed paper into wavy, fluted sheets.
From Pulp to Flutes
- The process begins with pulping, where wood fibers or recycled paper are broken down and cleaned.
- Once formed into sheets, the medium is passed through heated rollers, imprinting the iconic corrugated pattern.
Strength Through Design
The fluted medium’s shape is not just aesthetic. Its arches distribute weight evenly, making it ideal for shipping heavy or delicate items.
Step 3: Forming the Corrugated Board – A Symphony of Layers
The Layering Process
Machines precisely align the medium between two linerboards using starch adhesives. This “sandwich” structure is key to the box’s strength, with each layer playing a vital role in its performance.
Heat and Pressure: The Unseen Heroes
Controlled heat and pressure ensure the adhesive sets firmly, providing durability and stability. This step also contributes to water resistance, crucial for boxes exposed to moisture during shipping.
Combining Linerboard and Medium: Crafting the Corrugated Board
Here’s where the magic happens. Combining the fluted medium with linerboard results in the robust corrugated board we know.
Bonding for Strength
- Adhesives, often starch-based, are applied to the fluted medium.
- Linerboards are pressed onto both sides, creating a sandwich of strength.
Precision Matters
Temperature and pressure are critical here. Too much adhesive or uneven pressing can weaken the box, while optimal conditions ensure longevity and reliability.
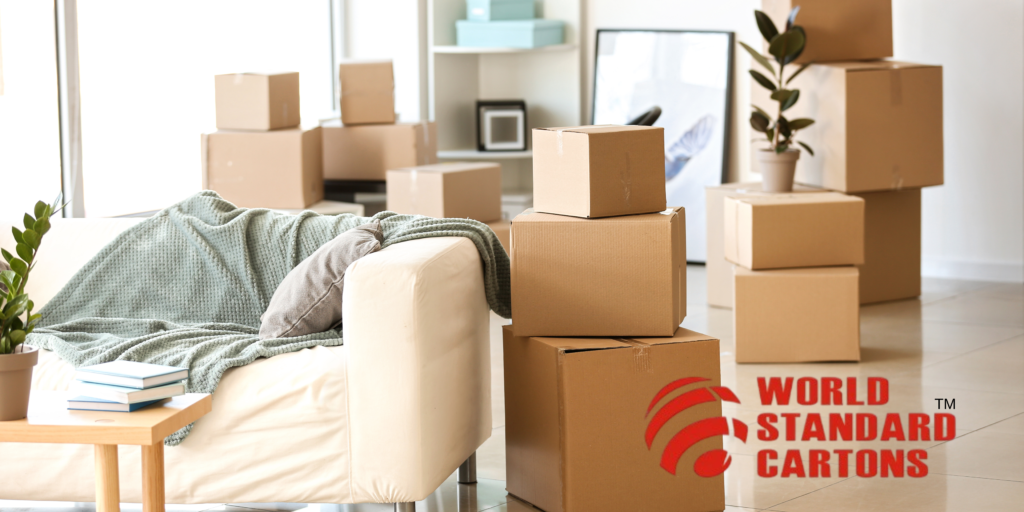
Step 4: Cutting and Scoring – Tailoring for Versatility
Automation and Precision
Modern die-cutting machines can produce intricate box designs with extreme accuracy, accommodating everything from pizza boxes to industrial crates.
Sustainability in Cutting
Scraps and leftover materials from this step are collected and recycled, ensuring minimal waste. Some manufacturers also repurpose offcuts into protective fillers.
Cutting and Scoring: Shaping the Future
After forming the corrugated board, it’s time to shape it into boxes. This stage is where versatility comes alive.
Die Cutting
Using custom dies, large sheets of corrugated board are cut into specific shapes. This step enables intricate designs like locking tabs or handles.
Scoring for Precision
Scoring creates fold lines, ensuring the box folds perfectly during assembly. Imagine receiving a package where the box won’t stay closed—scoring prevents this.
Step 5: Printing and Branding – Elevating the Ordinary
The Psychology of Packaging
Studies show that 72% of consumers say packaging design influences their purchasing decisions. Vibrant, well-branded corrugated boxes help businesses stand out.
Digital Printing Innovations
Traditional flexographic printing is now complemented by digital printing. Digital techniques allow for smaller print runs, personalized designs, and faster turnarounds, benefiting e-commerce and subscription box services.
Eco-Friendly Inks
Water-based and soy-based inks are replacing solvent-based options, reducing harmful emissions during production.
Printing and Branding: Making an Impression
Corrugated boxes are more than functional; they are powerful branding tools. Companies leverage printing to make their boxes visually appealing.
Flexographic Printing
This technique uses flexible plates to apply vibrant inks. From minimalist designs to detailed graphics, flexographic printing offers versatility.
Customization Matters
Brands can showcase their identity through logos, slogans, and product details. A beautifully printed box enhances unboxing experiences, a crucial trend in e-commerce.
Step 6: Folding and Gluing – Assembly in Motion
Beyond Glue: Alternative Joining Techniques
While adhesives are most common, innovations like ultrasonic bonding are emerging, which use high-frequency vibrations to join materials without chemicals.
Meeting Custom Needs
Boxes can be tailored for specific industries:
- Retail Displays: Folded into attractive shapes for in-store promotions.
- E-Commerce: Designed with tear strips and reclosable flaps for convenience.
Folding and Gluing: Assembling the Puzzle
Boxes come to life during folding and gluing. Machines precisely fold the scored sheets and glue seams to form box shapes.
Automation in Action
High-speed machines ensure uniformity, folding and gluing hundreds of boxes per minute. This efficiency is vital in meeting high demand.
Strength at the Seams
While adhesives are common, metal staples may be used for heavy-duty applications. This flexibility caters to industries requiring extra durability.
Step 7: Quality Control and Packaging – The Final Check
Rigorous Testing
Boxes undergo strength tests such as:
- Bursting Strength Test: Ensures the box can withstand external pressure.
- Edge Crush Test (ECT): Assesses stacking strength.
Automation in Inspection
AI-driven systems now detect even the slightest defects in printing, cutting, or bonding, minimizing human error and ensuring consistency.
Quality Control and Packaging: Ensuring Excellence
The final step is all about perfection. Every box undergoes rigorous checks before leaving the factory.
Inspection Protocols
Inspectors check for defects like uneven cuts, weak adhesives, or misaligned prints. Advanced technologies, such as AI-driven quality control, are revolutionizing this stage.
Preparing for Shipping
Boxes are bundled, labeled, and prepared for transport. Efficient packaging ensures they arrive at their destination ready for use.
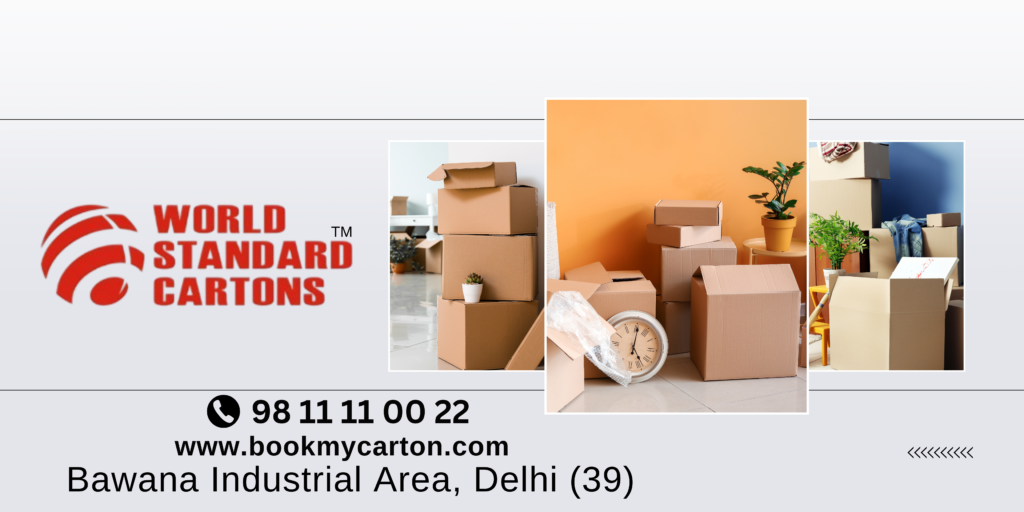
Beyond the Basics: Innovations in Corrugated Box Manufacturing
The corrugated box industry is evolving rapidly. Manufacturers are exploring new materials, enhancing durability, and adopting digital printing technologies. These innovations are shaping the future of packaging.
1. Sustainable Practices
The push for biodegradable adhesives and water-based inks is making corrugated boxes even more eco-friendly. Some companies are experimenting with plant-based coatings for water resistance.
2. Smart Packaging
Imagine a box that tracks its location or monitors humidity levels. With embedded sensors, smart corrugated boxes are becoming a reality.
The Environmental Footprint of Corrugated Boxes
Sustainability: A Core Principle
Corrugated boxes are a cornerstone of sustainable packaging due to their recyclability and minimal environmental impact. Today, many manufacturers operate with a closed-loop system, where used boxes are collected, recycled, and reprocessed into new corrugated material.
- Recycling Rates: In the U.S. alone, corrugated boxes have a recycling rate of over 90%, making them one of the most successfully recycled products.
- Energy Savings: Recycling corrugated materials saves significant energy compared to producing new paperboard. This reduces the industry’s carbon footprint.
Eco-Friendly Innovations
- Bioplastics: Some manufacturers are experimenting with integrating biodegradable plastics into corrugated boxes for increased durability while maintaining sustainability.
- Recycled Coatings: New water-resistant coatings derived from bio-based sources are reducing reliance on petroleum-based products.
Industry-Specific Use Cases
E-Commerce Packaging
The e-commerce boom has redefined corrugated box design:
- Unboxing Experience: Custom designs enhance branding and customer engagement during the unboxing process.
- Return-Friendly Designs: Boxes with tear strips and resealable adhesive help streamline returns, an essential feature in online retail.
Food Packaging
Food-grade corrugated boxes are designed to:
- Maintain freshness during transport.
- Meet strict FDA standards for direct contact with consumables.
- Reduce waste with biodegradable inner linings.
Heavy-Duty Applications
Industries like automotive and aerospace rely on corrugated boxes for:
- Custom Inserts: Protective inserts ensure the safety of high-value components.
- Reinforced Designs: Double-wall or triple-wall corrugated structures handle heavy loads efficiently.
Economic Impact and Job Creation
The corrugated box industry is a significant contributor to the economy:
- Employment: From raw material sourcing to manufacturing and distribution, the sector employs thousands globally.
- Local Economies: Many paper mills and box manufacturing plants are integral to the economies of rural areas, supporting local communities.
- Exports: Corrugated boxes are vital in exporting goods, helping local businesses expand into international markets.
Technological Advancements in Manufacturing
Automation and Robotics
Robotics is streamlining the production process, increasing efficiency, and ensuring precision in cutting, scoring, and assembling corrugated boxes. Automated guided vehicles (AGVs) also improve logistics within factories.
Digital Twin Technology
Digital twins allow manufacturers to simulate production processes, optimize workflows, and predict maintenance needs, reducing downtime and waste.
AI in Quality Control
AI-powered systems detect even minute defects, ensuring that every box leaving the factory meets the highest standards of quality.
The Role of Corrugated Boxes in Marketing
Corrugated boxes are no longer just protective containers; they are powerful marketing tools. Companies use custom designs and printing to:
- Build brand recognition with bold logos and colors.
- Communicate product details and benefits directly on the box.
- Enhance retail presence with aesthetically appealing packaging.
Global Trends Shaping the Industry
Regional Growth
- In developing regions, the demand for corrugated boxes is rising due to expanding e-commerce and manufacturing sectors.
- Developed nations are focusing on innovation and sustainability to cater to environmentally conscious consumers.
Material Shortages
Global supply chain disruptions have occasionally led to shortages in raw materials, pushing the industry to explore alternatives like agricultural waste and synthetic fibers.
Consumer Preferences
As consumers increasingly prioritize eco-friendly packaging, businesses must align their packaging strategies to meet these expectations, further driving innovation in the industry.
Broader Applications of Corrugated Boxes
Corrugated boxes are not just for shipping. They are used in:
- Agriculture: To store and transport fresh produce.
- Electronics: Offering anti-static variants to protect sensitive components.
- Food Industry: With food-grade coatings for direct contact with edibles.

Challenges in the Industry
- Supply Chain Pressures: Increasing demand for packaging during e-commerce booms strains raw material supplies.
- Environmental Regulations: Adhering to stricter rules on emissions and waste management requires constant innovation.
- Cost Management: Balancing sustainability with affordability is a persistent challenge.
- Raw Material Volatility: Fluctuating prices of paper and adhesives can strain profit margins.
- Environmental Regulations: Meeting stricter emissions and waste standards requires ongoing investment.
- Global Competition: Competing with international suppliers necessitates efficiency and cost-effectiveness.
Future Trends in Corrugated Box Manufacturing
- Smart Packaging: QR codes, RFID tags, and NFC technology will make boxes interactive, helping with inventory tracking and consumer engagement.
- Biodegradable Coatings: Research is advancing on water-resistant coatings that break down naturally, eliminating traditional plastic liners.
- Closed-Loop Systems: More companies are adopting systems where used boxes are collected, recycled, and transformed into new products within the same supply chain.
- Circular Economy: Advancements in recycling and waste reduction will further solidify corrugated boxes as eco-friendly champions.
- Biodegradable Adhesives: Innovations in adhesives derived from natural sources will make boxes even more sustainable.
Corrugated Boxes: A Pillar of Circular Economy
Corrugated boxes epitomize sustainability through their recyclability and reusability. By participating in a circular economy, they reduce the need for virgin resources and help combat waste.
The Bigger Picture: Why Corrugated Boxes Matter
Corrugated boxes aren’t just products; they are enablers of commerce and sustainability. They support industries, protect goods, and reduce waste through recyclability. As packaging needs grow more sophisticated, these boxes remain a cornerstone of innovation.
Conclusion
The story of a corrugated box is one of transformation. From raw materials to a finished product, every step in the manufacturing process is a testament to human ingenuity and a commitment to sustainability. Understanding this journey enriches our appreciation for these ubiquitous yet indispensable creations.
As the world moves towards greener and smarter packaging solutions, the corrugated box continues to adapt, proving that even the simplest products can have a profound impact. Whether you’re a business owner or an eco-conscious consumer, understanding how corrugated boxes are made can inspire you to make informed choices that benefit both your operations and the planet.
Corrugated boxes may seem mundane, but their production involves a blend of craftsmanship, science, and environmental responsibility. They are silent yet essential partners in global commerce, ensuring goods move safely and sustainably.
As consumer preferences shift towards greener, smarter solutions, the humble corrugated box is evolving. Whether you’re a business seeking innovative packaging or a consumer appreciating sustainable choices, these boxes are worth celebrating for their vital role in a sustainable future at bookmycarton.
Follow us on: Instagram, Facebook.
Our Channel: @bookmycarton.